Product
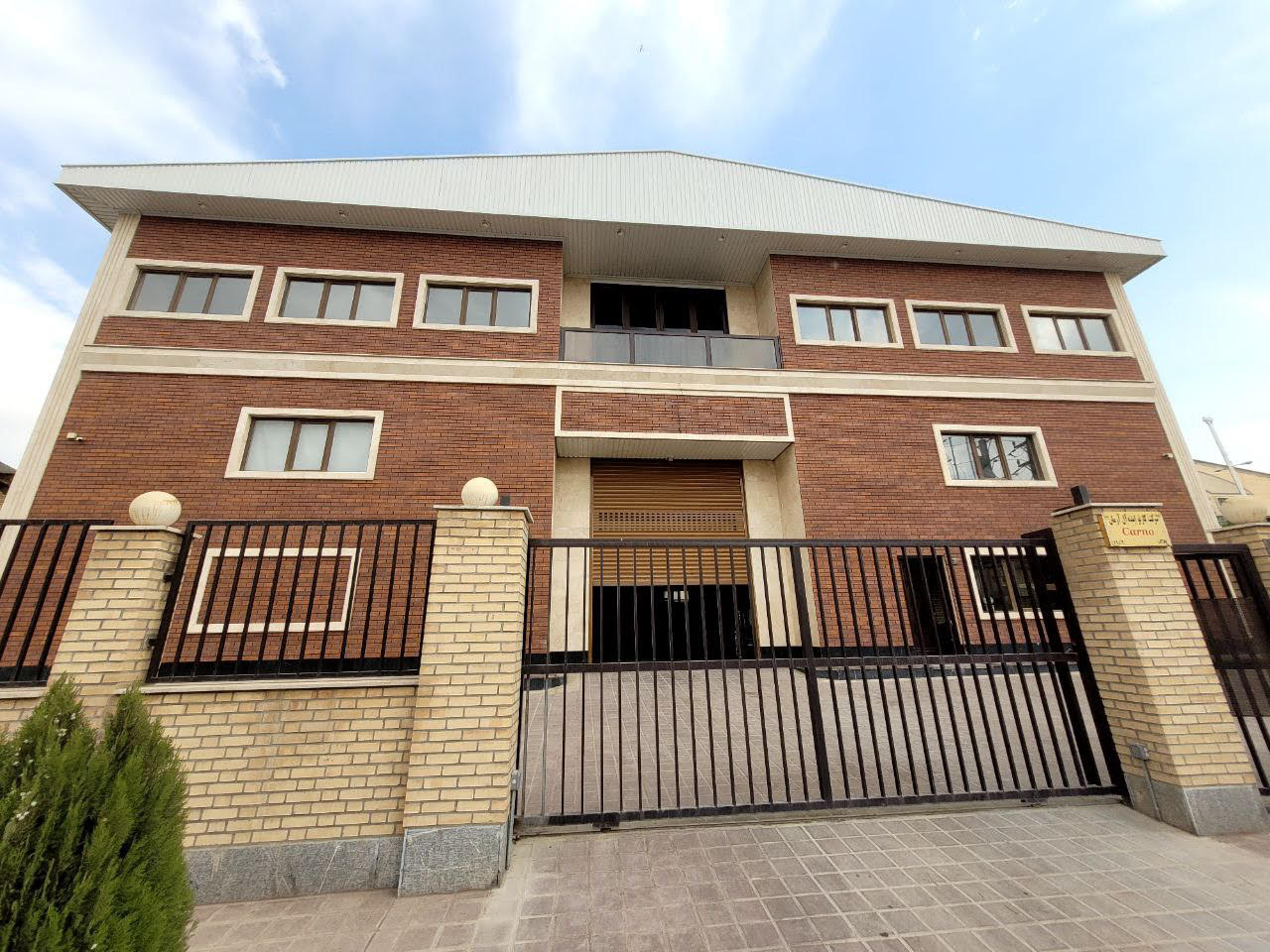
About Carnocast
Carno Ideal Arman Knowledge-based Co. was established in 2008. Since its establishment, this company was established in Sharif Advanced Technology Incubator (Sharif Technology University Techno-Park) due to its innovative and knowledge-based activities. Having great achievements and successes in various industries sectors including the energy, oil, gas and railway equipment industries, Carno Co. has developed its hardware and software by relying on knowledge, expertise, initiative, and innovation.. Now, by focusing on reverse engineering, it has followed a successful path in designing, manufacturing, and overhauling rotating equipment and turbomachinery’s focus on gas turbines and turbochargers.
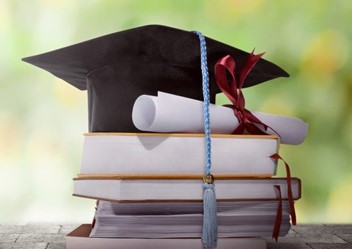
Master's project in the field of vacuum investment casting
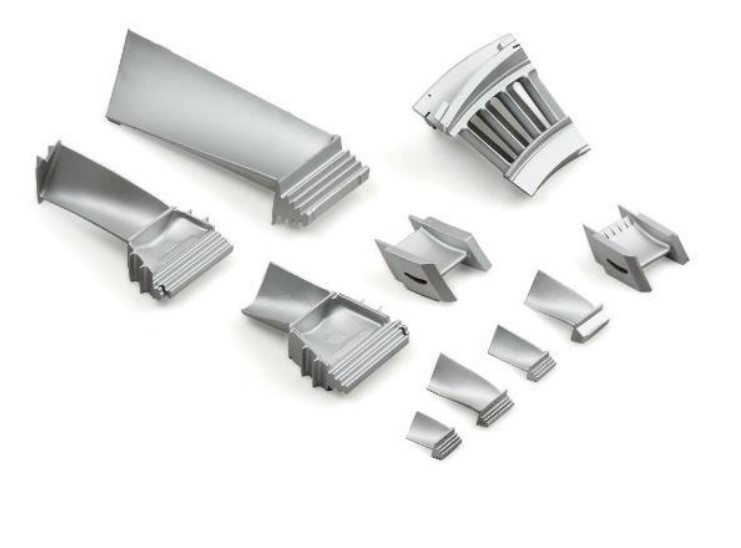
Management of several projects in the field of casting blades
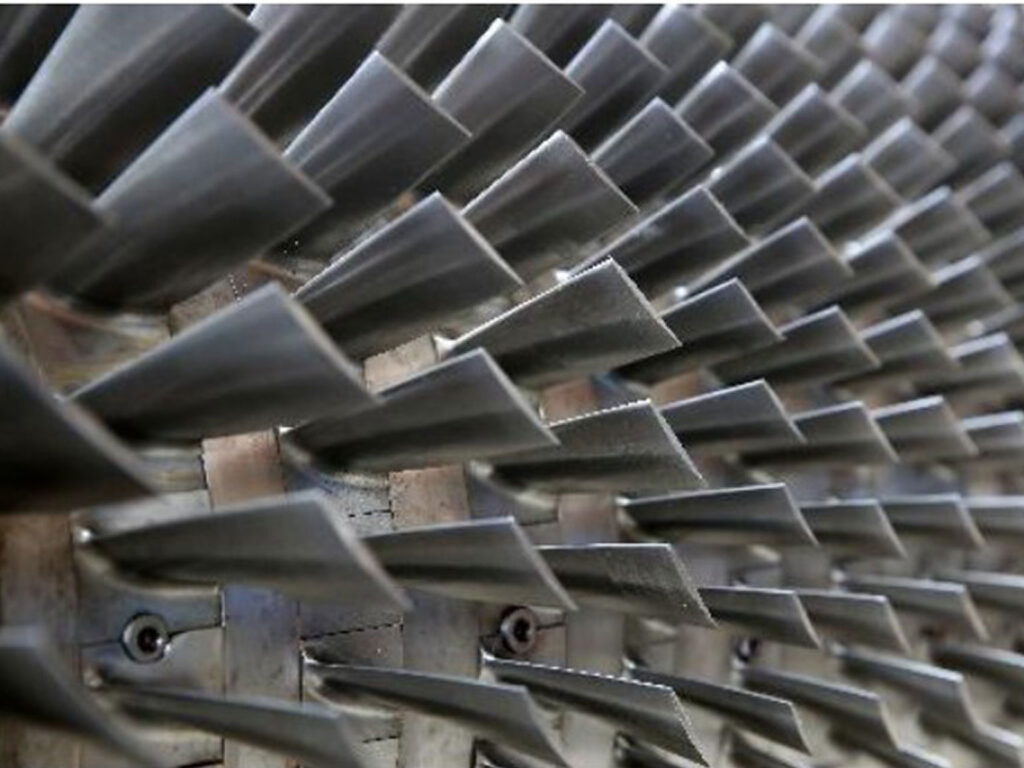
Management of several projects in the field of casting blades
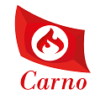
Establishing a knowledge-based company in Carno
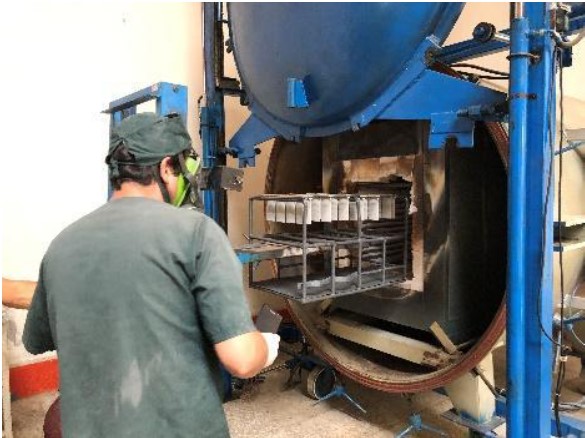
Renovation and rejuvenation of gas turbine blades begins
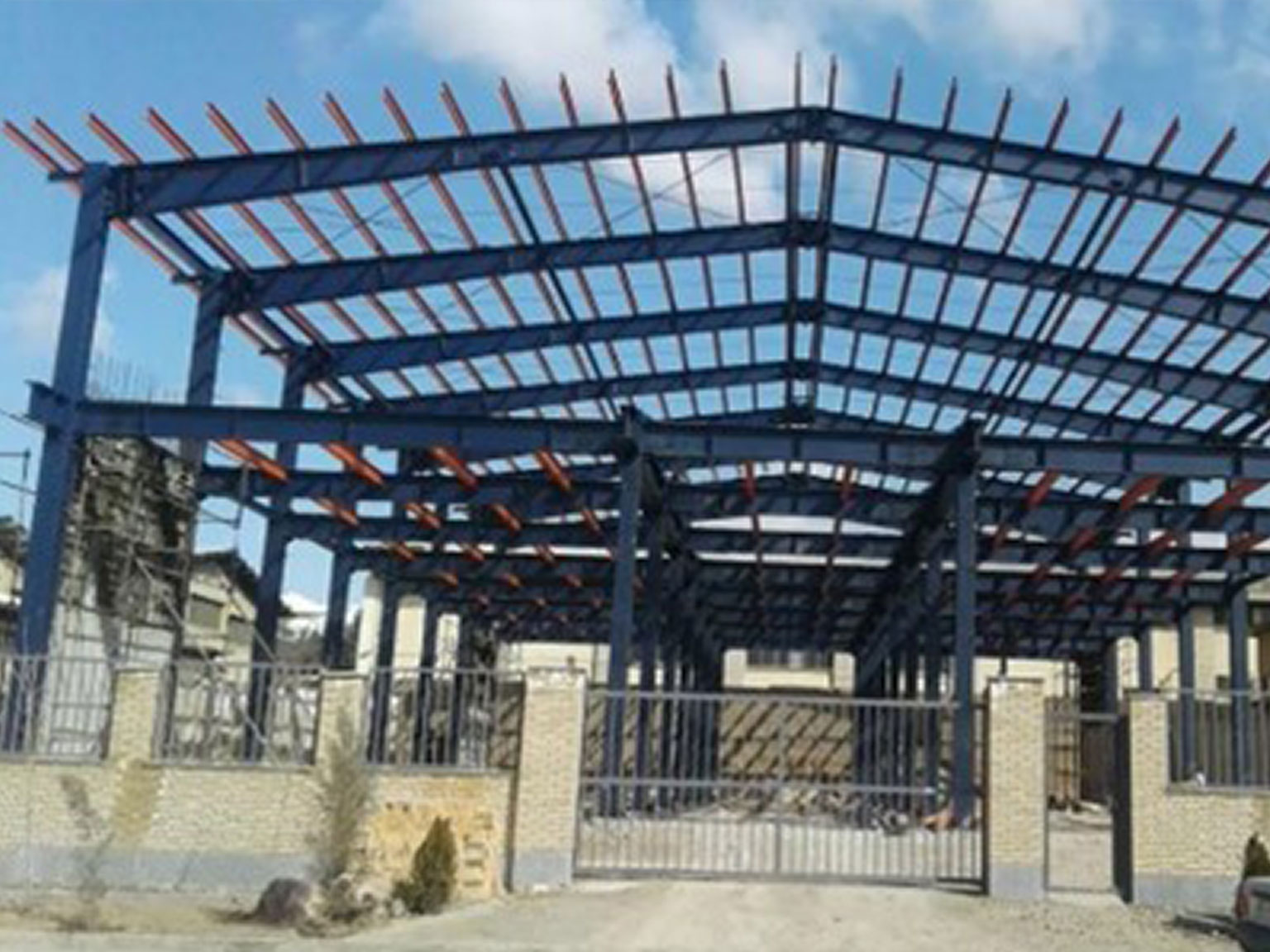
Factory construction and installation of equipment
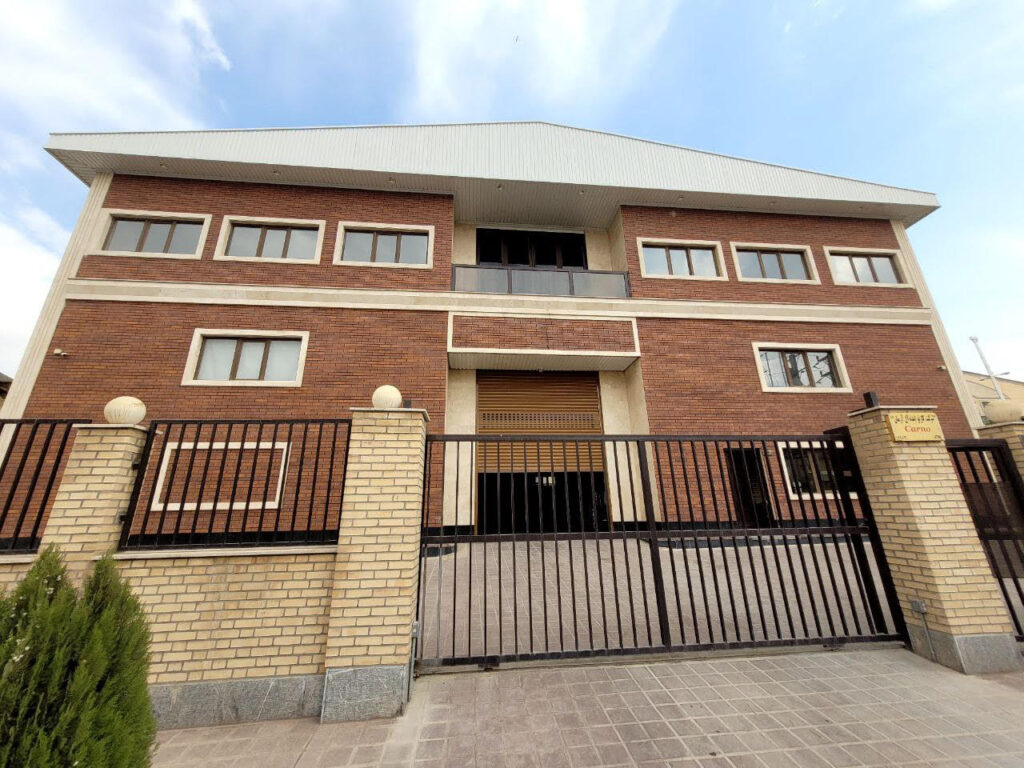
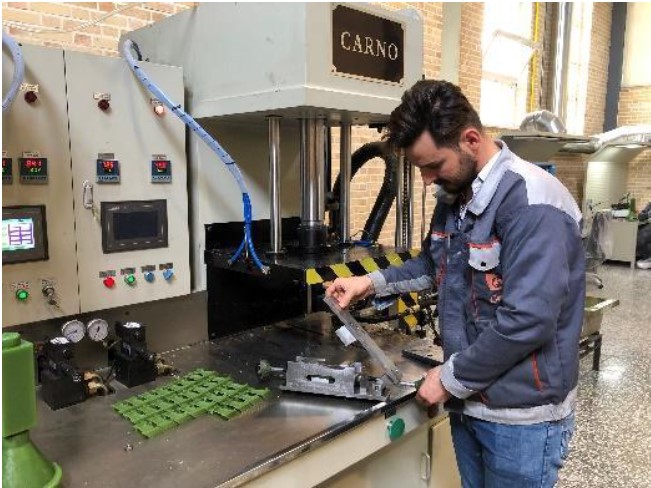
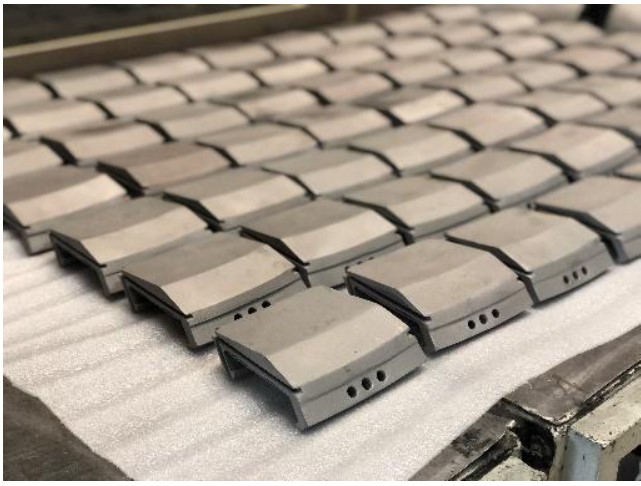
Articles
Vacuum Investment casting applications
Vacuum Induction melting furnace (VIM)
Faq
Most alloys and metallic materials have investment casting ability. Plain carbon steels, alloy steels, stainless steels, superalloys, colored metals, etc. can be poured by investment casting method.
Complex geometrically shaped parts that cannot be machined easily or have an expensive machining cost are easily shaped by investment casting method. Small parts, complex parts, difficult to machine parts, and precision components can be cast by investment or precision casting process.
Rapid production, small and complex parts, accurate dimensions, negligible machining need, internal channels production ability, and economy of scale are some pros of investment casting.
The disadvantages of investment casting include the initial time for designing and manufacturing wax injection molds, high primary production costs, disposable wax models, and ceramic shells.